Everything about Alcast Company
Everything about Alcast Company
Blog Article
Top Guidelines Of Alcast Company
Table of ContentsThe 10-Minute Rule for Alcast Company9 Simple Techniques For Alcast CompanyFascination About Alcast CompanyThe 30-Second Trick For Alcast CompanyAlcast Company Things To Know Before You Get ThisThe Ultimate Guide To Alcast Company
The subtle distinction hinges on the chemical web content. Chemical Comparison of Cast Aluminum Alloys Silicon advertises castability by minimizing the alloy's melting temperature level and improving fluidness throughout casting. It plays an essential duty in permitting elaborate molds to be loaded precisely. Additionally, silicon adds to the alloy's strength and wear resistance, making it beneficial in applications where longevity is crucial, such as automotive components and engine elements.It additionally boosts the machinability of the alloy, making it much easier to refine into ended up items. This way, iron adds to the general workability of aluminum alloys. Copper increases electric conductivity, making it useful in electric applications. It additionally enhances corrosion resistance and adds to the alloy's total toughness.
Manganese adds to the stamina of light weight aluminum alloys and enhances workability. Magnesium is a light-weight element that gives toughness and impact resistance to light weight aluminum alloys.
8 Simple Techniques For Alcast Company
Zinc improves the castability of light weight aluminum alloys and aids regulate the solidification process throughout casting. It enhances the alloy's stamina and firmness.
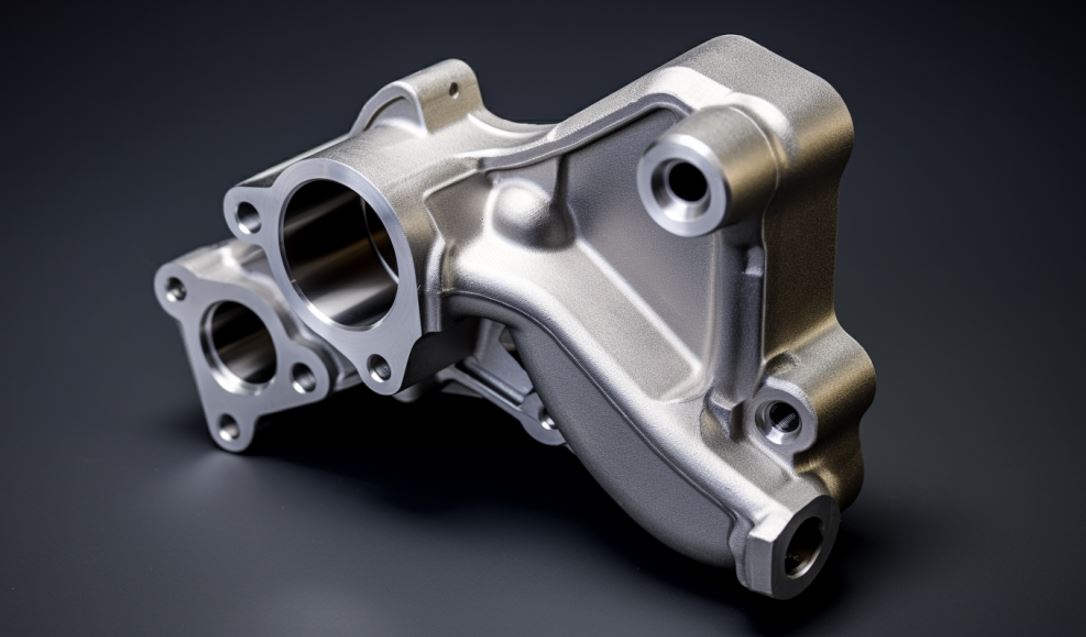
The primary thermal conductivity, tensile strength, return stamina, and prolongation differ. Select suitable resources according to the efficiency of the target product generated. Amongst the above alloys, A356 has the highest possible thermal conductivity, and A380 and ADC12 have the lowest. The tensile limit is the opposite. A360 has the very best return strength resource and the highest possible elongation price.
Things about Alcast Company
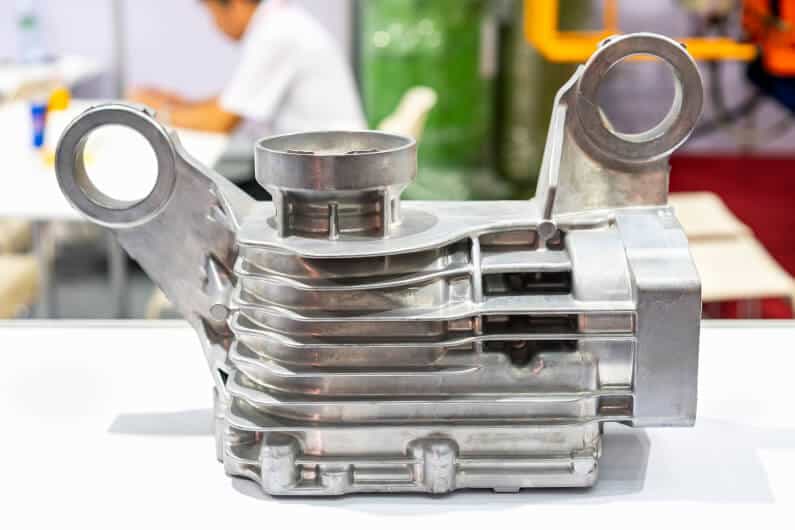
In accuracy spreading, 6063 is fit for applications where elaborate geometries and premium surface finishes are vital. Instances include telecommunication rooms, where the alloy's superior formability enables smooth and cosmetically pleasing layouts while preserving architectural stability. Likewise, in the Illumination Solutions market, precision-cast 6063 elements develop sophisticated and reliable illumination components that need complex shapes and excellent thermal efficiency.
The A360 exhibits superior prolongation, making it ideal for complex and thin-walled parts. In accuracy casting applications, A360 is well-suited for markets such as Customer Electronics, Telecommunication, and Power Devices.
Not known Facts About Alcast Company
Its one-of-a-kind buildings make A360 an important selection for precision spreading in these markets, boosting product sturdiness and top quality. Aluminum Castings. Aluminum alloy 380, or A380, is an extensively used casting alloy with a number of distinct attributes.
In precision spreading, aluminum 413 shines in the Consumer Electronics and Power Devices industries. This alloy's exceptional rust resistance makes it a superb option for exterior applications, guaranteeing resilient, resilient items in the discussed markets.
Alcast Company Things To Know Before You Get This
The aluminum alloy you pick will substantially influence both the spreading procedure and the properties of the final product. Because of this, you should make your choice meticulously and take an educated method.
Figuring out the most appropriate light weight aluminum alloy for your application will indicate evaluating a large range of attributes. The initial category addresses alloy characteristics that influence the production process.
The Single Strategy To Use For Alcast Company
The alloy you pick for die casting directly influences a number of facets of the spreading procedure, like how easy the alloy is to work with and if it is vulnerable to casting issues. Warm breaking, likewise called solidification breaking, is a typical die casting flaw for light weight aluminum alloys that can cause inner or surface-level tears or fractures.
Specific light weight aluminum alloys are much more prone to hot breaking than others, and your selection needs to consider this. Another common issue located in the die casting of light weight aluminum is die soldering, which is when the cast adheres to the die walls and makes ejection tough. It can harm both the cast and the die, so you need to search for alloys with high anti-soldering buildings.
Corrosion resistance, which is currently a significant feature of aluminum, can vary significantly from alloy to alloy and is a crucial characteristic to think about depending upon the environmental problems your product will certainly be revealed to (aluminum casting manufacturer). Put on resistance is one more residential property typically sought in aluminum items and can differentiate some alloys
Report this page